日前,石油壹号编辑获悉:巴斯夫将新型材料Elastolit® 8819首次应用于高端车型的零部件上,并实现批量生产。此种新工艺在大幅减轻零部件重量的同时,还能在确保安全性的前提下降低汽车燃油消耗。据悉,此次研发成果是建立在巴斯夫与STR Automotive深度合作上。此前巴斯夫通过降低零部件厚度,或使用特殊填料组合以及相应较低密度材料来减轻重量的尝试均告失败,因为所得零部件机械强度、刚度和冲击强度等机械性能不足。对此,STR Automotive为巴斯夫提出了解决方案,即采用耐高温、刚度高、冲击强度好的高模量PU基料。
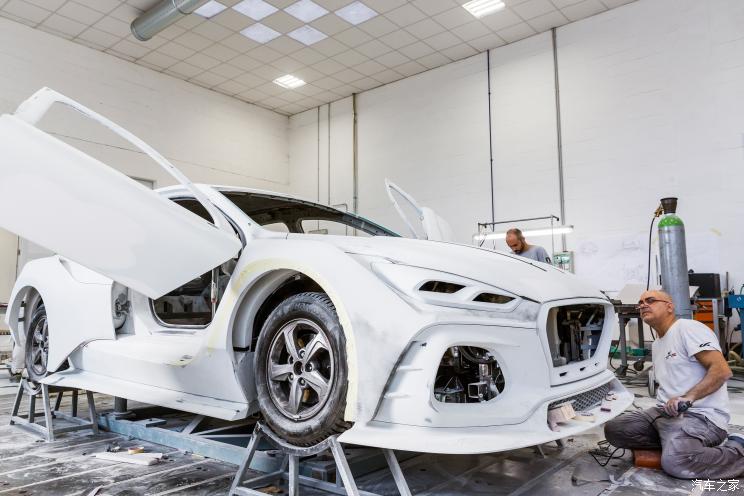
根据相关数据显示,在采用相同动力系统和传动系统的前提下,乘用车的整车质量每减少10%,燃油消耗就可降低6%-8%。因此,不论是传统燃油车还是新能源汽车,整车的轻量化设计目前是一个势在必行的趋势。
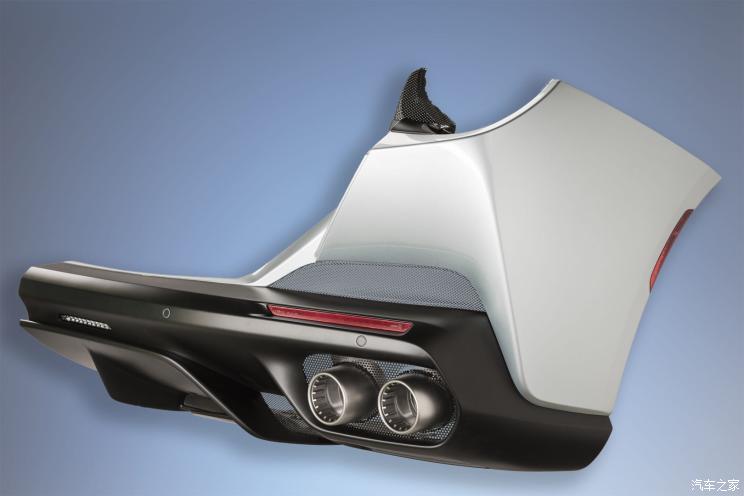
巴斯夫意大利S.p.A特性材料部经理Guiseppe Monaco表示:“STR Automotive作为一个创新公司,可在现有零部件材料开发的早期阶段提供支持。”根据不同需求和应用情况,新型材料可与不同的填充材料组合,应用于汽车后保险杠、侧板、发动机舱以及具有特殊减重需求的零部件。在第一批使用该新型材料制造的系列零部件中,每平方米表面积的重量已经降低了600g。对于后翼子板而言,这意味着重量最多可减少1.5kg。
STR Automotive首席执行官Massimo Cecchini对此表示:“通过组合全新材料和兼容的填料,可满足客户不同的需求。对于主机厂和用户来说,汽车减重不能以牺牲质量为代价,必须具备均衡的性价比。”